|
COIL COATING DIVISION |
This division of ours makes Neotech a single point for various requirements of all types of steel buildings and cladding by offering the client multiple choices in choosing cladding colours. |
Our state of the art production facility with a annual capacity of 60,000 tons can offer a range of colours to match every architectural design situation.Polyester,PVF2 coatings are available on galvanized steel,aluminum and zinc/aluminum alloy coated steel. |
|
|
ABOUT COIL COATING |
 |
Coil coating is a linear process by which protective organic coating are applied to flat metal sheets or strips packaged in rolls or coils.The metal strip is sent through a coating application station,where rollers coat one or both sides of the metal strip.The strip then passes through an oven where the coatings are dried and cured.As the strip exit's the oven, it is cooled by water spray again dried.
Neotech offers continuous coil coating liquid paint application on substrates such as Aluminum,Galvanized iron(GI),Galcalume(Aluzinc)using paint system such as plyester,PVDF,Plastisol and polyamides with colours of clients choice. |
This state-of -the -Art coil coating plant uses the technical colloboration from UK using best breed equipments from Italy,India,UK etc |
|
|
PRODUCT FEATURE |
 |
Note:This specification can be different according to the requirement of buyer.Some layers also can be omitted dur to the usage of products. |
Coating Systems: TMP/SMP/SDP/PVDF/PU/Epoxy etc..,capable of manufacturing in both uni-coat and multi-coat systems. |
|
|
CHEMICAL TREATMENT |
Removal of oil,crease washing and chemical treatment layer,this layer accomodates special layer that upgrades durability,corrosion resistance and adhesion on the surface of the substrate. |
|
PRIMER COATING |
This layer is an auxilary one that aims to give good adhesion through chemical interaction with grand layer on chemically-treated metal sheet.To improve corrosion resistance to corrosion,temperature and formability,it is specially coated with epoxy acrylic or plyester resin.Its coating thickness is approximately 5+/-micron. |
|
TOP COATING |
As a special coating layer of polyester or PVDF resin coated on the primer,this has a high degree of those properties including durability,anti-corrosion,chemical resistance,formablity and mechanical propety,as well as unique coating thickness due to highly sophisticated coating mehod and beautiful appearance.Itd coating thickness is approximately 20_/-micron. |
|
BACK COATING |
This is epoxy polyester type special coating that is coated on chemically-trated substrates.It puts great emphasis on the improvement of resistance to temperatue and corrosion of back side.Its thikness is approximately 5-7 micron. |
|
|
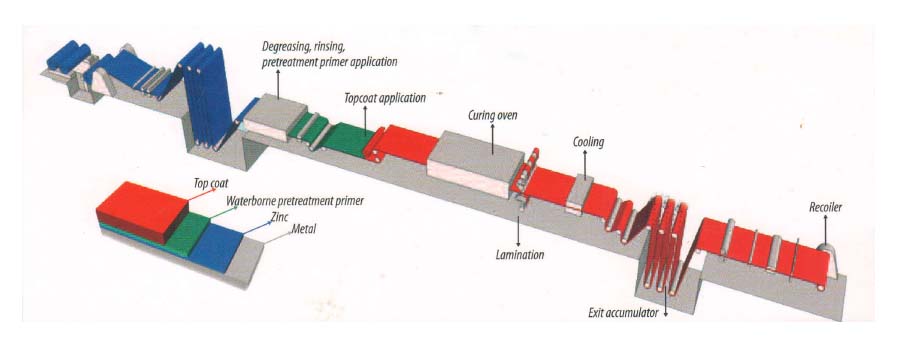 |
|
SPECIFICATIONS OF PRE-PAINTED COILS |
|
Galvanised Steel |
Galvalume |
Aluminum |
|
As per IS 277:2003 |
As per ASTM A 792/A 792M-08 |
Alloy AA 3105/8011 |
Tensil Strength |
240/350/550 Mpa |
350/550 / Mpa |
As per Alloy |
Thickness range(TCT) |
0.14-0.9 mm |
0.2-0.8 mm |
0.18-1.2 mm |
Width (mm) |
750-1250 mm
(Standard-1220 mm)
|
900-1200 mm |
750-1250 mm
(Standard-1220 mm) |
Coil weight (MT) |
3-6 MT |
3-6 MT |
2-3 MT |
Coil ID |
508 mm/610 mm |
508 mm/610 mm |
508 mm/610 mm |
Metal Coating |
120 GSM or higher as per customer specifications |
AZ70-AZ150 or as per customer specifications |
None needed |
|
|
Primer (microns) |
Upto 8 microns. |
Back Coat (microns) |
Upto 8 microns. |
Top Coat (microns) |
Upto 18-20 microns.(Above caoting thickness are standard and any specific requirements can also be coated). |
Guard film(Optional) |
40 microns or as per customer specifications. |
|
 |
|
|
PHYSICAL CHARACTERSTICS (POLYESTER) |
PHYSICAL CHARACTERSTICS (PVF2) |
Typical Applictions |
Typical Applictions |
Roofing,walling,ceiling Components |
Roofing,walling,ceiling Components |
Typical Properties of Coating |
Typical Properties of Coating |
Nominal Total Dry Film Thickness 20 |
Nominal Total Dry Film Thickness 20 |
Scratch Resistance IS 101 |
Scratch Resistance IS 101 |
1500gms |
1500gms |
Flexbility (No Crack) Reverse Impact |
Flexbility (No Crack) Reverse Impact |
IS 14246:1995
40 in/ibs |
IS 14246:1995
40 in/ibs |
Bend Diameter |
Bend Diameter |
2T Is 4266:1995
(T=Substrate Thickness) |
2T Is 4266:1995
(T=Substrate Thickness) |
Corrosion Resistance |
Corrosion Resistance |
1 Salt Spray EAAC-T-F
750 hours |
1 Salt Spray EAAC-T-F
750 hours |
2 Humidity ECCA-T-F |
2 Humidity ECCA-T-F |
1000-hours |
1000-hours |
QUV Weathering Test
|
QUV Weathering Test |
1000 hours ECCA-T-10 |
1000 hours ECCA-T-10 |
Colours Available |
Colours Available |
Wide range of request |
Wide range of request |
Substrates available |
Substrates available |
GI/GL/Aluminium |
GI/GL/Aluminium |
Products Strengths |
Products Strengths |
Good exterior durability.Good Flexibility and Temperatue stability. |
Good exterior durability.Good Flexibility and Temperatue stability. |
Product Limitations |
Product Limitations |
Medium life product which exhibits Slight chalking and colour change in high UV environments. |
Excellent resistance to animal,Vegetable fats and oils,petroleum oils and aliphatic Hydrocarbons.Good stain resistance.Good Colour retention.The inert fluorine modified Coating is based on Kynar 500 resin developed by Pennwalt Corporation. |
Life to first maintenance |
Life to first maintenance |
In most temperate environments a life to first maintenance of the coating of 5-7 years can be expected |
In most temperate environments a life to first maintenance of the coating of 5-7 years can be expected |
|
|
TESTING PROCESS |
Test |
Results |
Test Method |
Resistance to Chemical Corrosion(5% NaOH & 5% H2S04) |
Good |
ECCA-T-18 |
Solvent rub(MEK) |
Min 100 double rub |
AICC-23 |
Erichsen cupping test |
>6 mm |
Is-10175 (82) |
Gloss at 60 degrees depending on finish |
80-85/25-30 |
ECCA-T-4 |
|
|
APPLICATIONS |
These pre coated coils find their applications in the Roofing & Cladding,Building Materials,Ceilings,Rolling Shutters,Furnitures,Cold storage,Automotives,White goods to name a few.Particularly for the construction industry we can offer widest range of colours.There is an attractive solution to every architectural design solution.(to be moved after specifications) |
 |
|
|
NUMBER OF WAYS COIL COATING IS SUPERIOR ToOther PAINT APPLICATION PROCESS |
1. |
Environment Friendly |
 |
2 |
Cost-Effective |
3 |
Uniformity Of Paint Thickness |
4 |
Superb Automotive Type Finish |
5 |
Outstanding Adhesion Properties |
6 |
Durable And Long Lasting |
7 |
Easy To Use Forming And Fabricating |
8 |
Available In Wide Range Of Colours |
9 |
Numerous Different Paint System |
10 |
Proper Coating Of Edges |
11 |
Superiors Resistance Of Corrosion |
12 |
Efficient Process With Less Wastage |
13 |
Consumes Less Energy Than Conventional Process |
14 |
Easy Recycling Of Process Materials |
15 |
Gives A Continuity Of Colour |
16 |
Practical And Efficient System. |
|